气凝胶通常来源于湿凝胶,其本身通过溶胶-凝胶工艺制备,并使用超临界流体(最常见的是CO2)进行干燥、冷冻干燥或蒸发干燥。包括聚合物、生物聚合物和金属氧化物在内的多种材料都可以转化为气凝胶。
然而,其复杂的制造、高脆性和脆性结构极大地限制了它们的实际应用。为了解决脆性和刚性问题,已经使用了不同的技术来将柔韧性纳入气凝胶材料中。因此,引入了“柔性气凝胶”一词。迄今为止,柔性气凝胶可分为“混合柔性气凝胶”和“单组分柔性气凝胶”。
本文旨在提供柔性混合和柔性单组分气凝胶领域的最新突破、评估目前用于生产柔性混合和单组分气凝胶的技术、影响其柔韧性的因素,以及它们的局限性和不同的干燥方法(超临界干燥、冷冻干燥和环境压力干燥)。
二氧化硅的易碎性仍然是试图实现气凝胶高机械强度的不可避免的障碍。二氧化硅基气凝胶本质上是脆性的,这限制了它们的大规模应用。克服这一缺点的最有希望的方法是形成有机-无机杂化气凝胶。在这样的体系中,Si-O-Si贡献了无机部分,Si-C键代表有机部分;这种组合提高了气凝胶的疏水性,并提高了其机械强度。因此,有机-无机杂化气凝胶可用于特殊应用,例如在-40°C下进行太空探索的绝缘。
决定混合材料稳定性和性能的最重要因素是不同组件在制造过程中的集成方式。因此混合气凝胶的制备主要有两条路线:物理整合和化学整合。
在物理整合方法中,通过物理纠缠、氢键或范德华相互作用将功能组分掺入前体(生物聚合物或合成聚合物)中。然而,化学整合方法涉及在前体材料存在的情况下合成功能成分,这导致通过功能成分和聚合物之间的化学键产生更强的相互作用。
图1:
(a)气凝胶和柔性多孔PEDOT/SWCNT/BC薄膜的合成方法示意图。
(b)PEDOT/SWCNT/BC气凝胶和薄膜以及放置在蓬松羽毛上的轻质PEDOT/SWCNT/BC气凝胶的数字图像。
图2显示了混合气凝胶的物理外观(a)扭曲前和(b)扭曲后
纤维素纳米晶体(CNC)气凝胶由于晶体的刚度和单个晶体的流动性受限而自然易碎。传统上,低分子量交联剂已被用于增强气凝胶的韧性;然而,很少有人关注提高气凝胶的柔韧性。在此背景下,Zhou等人通过使用点击化学反应掺入功能聚合物,为开发具有优异机械性能和功能的纳米材料基气凝胶铺平了道路。
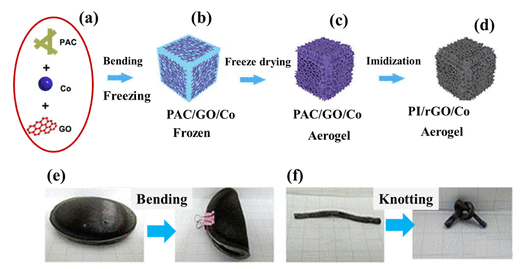
(a)显示气凝胶合成的示意图;(b)显示合成气凝胶的灵活性的图像;(c) PAC/GO/Co气凝胶,PI/rGO/Co气凝胶的原型;(d)在氮气气氛中在250 °C下亚胺化后获得的最终PI / rGO / Co气凝胶;(e)数字图像显示了弯曲过程中的优异柔韧性;(f)在打结过程中PI / rGO / Co气凝胶。
杂化气凝胶的柔韧性受两个主要因素的影响,即水凝胶的浓度和有机聚合物与交联剂的摩尔比。根据一项研究,当交联剂的摩尔比高于有机聚合物的摩尔比时,杂化气凝胶的柔韧性会增加。还得出结论,通过增加水凝胶的浓度,气凝胶的柔韧性也会增加。
通过在气凝胶的骨架上添加PMMA、木聚糖、PLA和纤维素酯等聚合物,可以提高气凝胶的抗压强度和柔韧性。然而,由于聚合物与气凝胶骨架之间的界面相互作用通常较低,气凝胶的尺寸稳定性和化学稳定性会降低。此外,这种聚合物共混技术不会显著改变组件之间的结构结合。因此,通常需要显著增加聚合物的浓度来增强杂化气凝胶的机械性能。
气凝胶最常见的是基于二氧化硅的。尽管其导热系数创下历史新低,但对于机械强度很重要的应用,二氧化硅气凝胶的脆性和脆性仍需改善。近年来,在开发涉及有机或纳米结构成分的气凝胶以改善机械性能方面取得了进展。另一方面,他们也可以将“固有柔性气凝胶”定义为由单一材料组成的气凝胶,这些气凝胶在给定温度下自然具有机械柔韧性,无需由其他成分改性。
近年来,科学家们专注于用有机聚合物而不是二氧化硅和金属氧化物等材料制造气凝胶。基于有机聚合物的气凝胶的一些例子包括由纤维素、聚氨酯、三聚氰胺/甲醛和间苯二酚/甲醛制成的气凝胶。然而,最近发现,与有机基杂化气凝胶相比,由单一工程聚合物成分(如PI或聚酰胺)生产的气凝胶具有更好的机械性能。
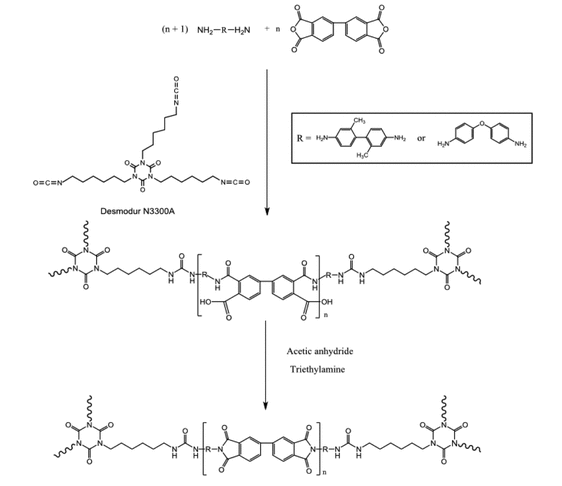
图五:
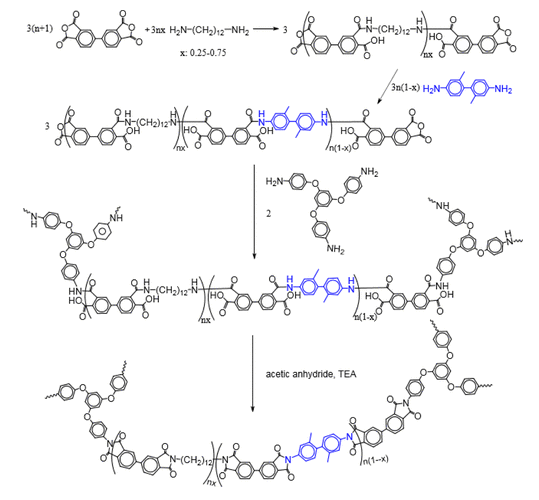
图六:

PI气凝胶合成原料示意图
PI低聚物的骨架结构在PI气凝胶中起着比交联剂更大的作用。不同的主链化学已被证明会导致加工收缩率的变化,从而导致密度和其他取决于密度的质量(包括模量和保湿性)的波动。通过调整前体溶液的浓度,也可以改变主链中具有相同化学性质的PI气凝胶的密度。
此外,单聚合物基气凝胶的柔韧性还受到其制造过程中采用的特定合成方法的影响。溶胶-凝胶聚合产生的气凝胶表现出基于聚合条件和交联剂的柔韧性变化。超临界干燥保留了聚合物网络的连通性,并降低了毛细管力,避免了结构坍塌。或者,使用常压干燥方法的溶剂蒸发(在大气压下从凝胶中蒸发)会导致结构崩溃。
在冷冻干燥过程中,单体的选择和溶剂的升华条件会影响所得聚合物气凝胶的柔韧性。此外,在气凝胶的合成过程中加入一些添加剂,如柔性聚合物,会产生柔软的成分和柔性结构。此外,一些特定的参数,如温度、生产时间、交联剂的共混和表面改性,可以根据所需的应用和具体特性(包括柔韧性)进行选择。
尽管聚酰胺(PI)气凝胶引起了世界各国的关注,但其实际应用仍然有限。这可能是由于交联剂价格昂贵且无法在商业上获得,这阻碍了它们的扩大规模。此外,合成方法涉及潜在的危险过程。这是阻碍单组分PI气凝胶大规模合成的两个关键因素。
众所周知,干燥方法对所得气凝胶的表面积和孔隙率有重大影响。干燥过程是气凝胶制造的最后也是最重要的阶段。由多糖聚合物形成的湿凝胶具有异质结构和充满水的高孔隙率。干燥过程的目的是消除滞留在孔隙内的液体。
冷冻干燥是一种额外的干燥方法,用于保护管网的孔隙率。该技术包括首先将孔隙液体冷却到其冰点温度,然后在真空下升华冷冻固体以在不损坏孔壁的情况下将其去除。通过这种方法开发的多孔结构被称为冷冻凝胶,它们的表面积和孔体积相对小于气凝胶。与超临界干燥类似,孔隙液应更换为凝固点和膨胀系数低的其他液体。然而,当孔隙液体在孔隙内结晶时,3D网络结构会崩溃。
冻干燥和超临界干燥方法不是气凝胶商业化生产的实用技术。然而,环境压力干燥方法对于气凝胶的大规模生产来说是简单且实用的。因此,使用了几种技术来排出周围环境中的孔隙流体,而不会导致管网收缩。事实上,为了减少作用在孔壁上的毛细管力,通常通过添加表面活性剂来增加孔壁和浇注液之间的接触角。
超临界干燥是传统干燥的另一种干燥方法,可以在保持孔隙率的同时产生气凝胶。它还保持了固体形式(干燥状态)湿凝胶的显着质地特征,并防止毛孔塌陷。在实践中,传统的超临界干燥需要将密闭容器中的湿凝胶加热到高于凝胶孔隙中溶剂临界值的温度和压力。
超临界干燥技术有两种:低温超临界干燥法和高温超临界干燥法。
超临界干燥装置示意图
用于多孔材料的干燥技术,如气凝胶、凝胶和泡沫,会对最终结构产生重大影响。干燥技术对孔隙率、机械强度、一般形态和孔径分布等特性有显著影响。多孔材料的孔径分布、机械稳定性和孔隙率都受到干燥技术的影响。超临界干燥通常会产生具有高孔隙率的维护良好的结构,而传统的干燥技术除了孔隙率降低外,还可能导致不同程度的结构改变。在选择干燥技术时,必须考虑精确的材料成分、预期功能和所需的结构特性。
上述所有技术都是有利的,但它们有其自身的局限性。冷冻干燥因其广泛的用途和优于超临界干燥的优势,例如易于应用、成本效益和适合开发高度结构化和有序的多孔气凝胶,因此更受欢迎。使用这种干燥技术可以在工业规模上制备许多气凝胶。
然而,它的缺点之一是溶剂蒸发对环境、人和动物造成的污染。超临界干燥体系是防止干燥收缩或介孔塌陷以获得表征良好的结构的有效方法。然而,在传统的超临界干燥过程中使用高温和高压,使用大量的溶剂,以及溶剂交换所需的时间,大大降低了它们扩大到工业规模的可能性。这种限制可能是由于该过程的整体成本很高,会增加能源和时间消耗。
摘选自:《柔性混合和单组分气凝胶:合成、表征和应用》|朗缪尔 (acs.org)
https://pubs.acs.org/doi/full/10.1021/acs.langmuir.3c01811
原文始发于微信公众号(艾邦气凝胶论坛):关于柔性混合和单组分气凝胶领域的合成、干燥技术详解