Blueshift的新型材料由85%的空气和15%的纯聚酰亚胺气凝胶组成,可在-200°C至2400°C以上的瞬态热传递中保护火箭、电池盒等的结构。
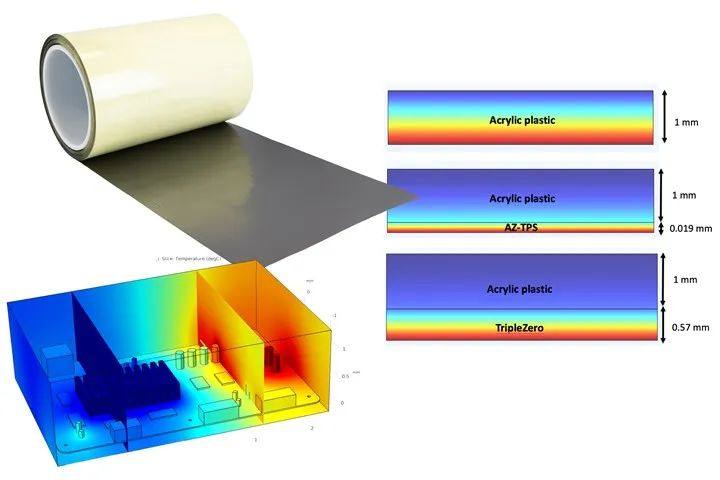
图1 AeroZero 即剥即贴 TPS(左上)是针对电池外壳(下图)和右图三个型号建模的,比较了亚克力板中的温度分布,其中不带 TPS 的底面施加恒定的300K(上图)、单层 AeroZero(中)和三层 TripleZero TPS(下图)。
空气化结构:TPS保护复合结构
航空航天与国防领域的技术革新正在彻底改变我们对机动性的传统认知。历史上,政府机构和大型商业集团——包括美国国家航空航天局(NASA)、波音公司、空中客车公司以及美国国防部——在开发新型飞行器上投入了巨额资金。然而,制造成本的高昂曾是小型私营企业进入这一行业的门槛。
2008年,随着SpaceX公司成功发射首枚火箭,市场格局开始发生根本性转变。原本由少数企业垄断的行业,逐渐演变为一个充满无数创新者的竞技场。这一变革持续推动着航天器和电动飞机领域的创新,使得低成本技术与高度复杂技术相结合成为可能,为整个行业带来了前所未有的活力和机遇。
位于美国马萨诸塞州斯宾塞市的Blueshift公司正是技术创新的典范。作为一家专注于深度技术的材料科学企业,Blueshift自2013年成立以来,一直致力于开发前沿产品。到了2020年,公司推出了其首款商业产品——一系列基于气凝胶的热保护系统(TPS),这些气凝胶由85%的空气和15%的纯净聚酰亚胺构成。这些TPS产品能够根据不同的热负荷事件,如空气加热、直接火焰加热或接触加热,进行个性化定制。
得益于其高孔隙性,这种材料显著降低了热能的传递速度,有效防止热量穿透到底层的复合结构中。产品轻薄的特性(从0.19mm的厚度开始)不仅便于实际应用,还为添加额外的功能层(例如石墨和包括铝在内的多种金属层)提供了空间。Blueshift的AeroZero品牌TPS产品系列,适用于包括碳纤维复合材料在内的多种表面,已经在火箭技术、电池、排气系统和电子设备等多个领域证明了其卓越的性能和有效性。
Blueshift公司的技术起源于一家知名电子公司面临的过热难题。“Blueshift公司总裁蒂姆·伯比回忆道:"我的合伙人加勒特·坡与多个团队合作,开发了一种制造聚酰亚胺气凝胶的工艺,并在实验室规模上成功进行了验证。尽管从实验室到规模化生产的过程需要大量资金和时间,但Poe和Burbey都深信这项技术的巨大潜力,特别是在航空航天领域。因此,他们决定在2013年成立Blueshift公司,致力于将这一创新技术转化为实际应用。”
Burbey将Blueshift公司已经商业化的技术命名为“空气化结构”。他强调,这种材料与传统的泡沫完全不同。“本质上,我们所做的是将空气以一种更加适合产品设计师使用的方式进行打包,”他解释道。这种材料拥有一个网络状的聚合物结构,但其中85%的空间被纳米级别的小气泡所占据——在材料的每个薄片上,这些气泡的数量超过了300万亿个。这种独特的结构不仅赋予了材料卓越的性能,也为设计师和工程师提供了前所未有的设计灵活性和创新可能性。
Burbey继续解释道:“许多人可能已经对二氧化硅气凝胶有所了解,但我们的产品与之截然不同。当我说‘空气化结构’时,我指的是一种兼具机械强度的材料。二氧化硅气凝胶虽然轻质,却缺乏足够的机械强度,不适合用于高振动环境。相比之下,我们的聚酰亚胺气凝胶在热保护系统(TPS)中的核心优势在于其能够与额外的基材结合——我们能够添加石墨、铝等层或其他材料,创造出具有强大功能性的复合产品。”这种创新的结合不仅提升了材料的适用性,也拓宽了其在各种工业应用中的潜力。
因此,Blueshift公司开发的热保护系统(TPS)能够替代那些陈旧的“vintage Apollo”时代的材料解决方案,显著提升航天器设计的效率与安全性。例如,Blueshift已经成功扩展了标准的185°C限值的环氧树脂和碳纤维复合材料的耐温范围,其工程设计的系统能够承受现代航空航天应用中从-200°C至超过2400°C的极端瞬态热负荷。这一技术突破不仅增强了材料的耐用性,也确保了在面对剧烈温度变化时的可靠性和稳定性。
“空气化结构”结构产生的原因
“空气在减缓能量和温度传递方面起着至关重要的作用。” Burbey解释道。“空气本身也是射频(RF)透明的,这一特性对于航空航天飞行器中集成的传感器和通信系统至关重要,因为它们需要无阻碍的信号传输。然而,空气的作用远不止于此。聚酰亚胺作为一种耐高温、耐化学腐蚀的高性能聚合物,其独特的分子结构在缓解多种热传递机制方面发挥着关键作用,包括热传导、对流和辐射热。这种材料的综合性能使其成为应对极端热环境的理想选择,为航空航天领域提供了一种创新的解决方案。”
图 2(a)传导是由于固体或液体中原子碰撞而传递的能量的结果。300K应用于底面。(b)对流是由于流体(液体/气体)分子的随机运动或整体运动而将热量从一个地方传递到另一个地方。300K应用于底面。(c)辐射是由于暴露于某一源发出的一定频率范围内的电磁波而产生的。热量从 25 千瓦的红外 (IR)灯传播到硅板。
Burbey说:“不论热能的来源如何,我们的材料均能有效阻挡热/冷流的传递。我们的空气与聚酰亚胺结合形成的骨架结构不仅减缓了热能的传入速度,还显著降低了热能的渗透率,即具有低热扩散性。这种结构同样导致了低热导率,也就是说,要改变材料的温度,需要更多的能量输入。”
他继续说道,“这些特性的结合,使我们的产品在应对瞬态热事件时表现出色。事实上,热传递的速度越快,面临的温度机制越极端,我们产品的效果就越显著。我们可以定制我们的产品,专门解决传导传热问题——传导传热往往会导致局部热点的形成——以及对流传热问题。对于辐射能,我们能够集成反射性顶层材料,例如具有高反射性的聚酰亚胺(VDA),进一步提升产品的热防护性能。”
建模与模拟
Blueshift公司的另外两项核心技术能力是建模和模拟。热缓解需求覆盖了广泛的应用场景,每个场景都有其独特的条件和要求。这些应用包括高速飞行器在5马赫至25马赫飞行速度下或重返大气层期间所面临的极端航空热负荷,以及电池热失控和发动机起火等紧急情况。
虽然不存在一种万能材料能够解决所有热管理问题,Blueshift通过对其材料进行精心的组合和定制,能够针对性地解决特定产品和车辆设计中的热管理挑战。这种高度定制化的方法确保了客户能够获得最适合其特定需求的热保护解决方案。
“建模和模拟是我们实现定制化解决方案的关键,”伯比强调。“解决方案的设计取决于多种因素,包括部件所处的具体环境、热源的类型——比如辐射加热与传导加热的区别——以及在配置中可利用的空间大小。材料将直接接触哪些物体,或者是否存在间隙?这些间隙对热传递有何影响?
此外,热负荷的持续时间和我们希望达到的热减少目标也是至关重要的考量因素。通过这些细致的分析和模拟,我们能够确保为每个独特的应用场景开发出最合适的热管理策略。例如,假设您所处的环境中火焰温度约为 1000ºC,暴露时间为 15 分钟。我们的客户的电子设备温度可能无法超过 200°C,因此我们可以对该系统进行建模,以确定最适合的产品来满足他们的要求。”
他补充说,这种解决方案不仅要保护电子设备,还要足够轻、薄,以尽量减少对整个车辆或产品设计的影响。Burbey 指出,Blueshift 还具备测试能力,包括火焰测试和各种材料级热分析,以验证建模结果。“最近,我们进行了各种火焰测试,以模拟电池应用中的热失控,”他说,“我们还必须开发有助于熔融颗粒和爆炸缓解的材料。”
多层堆叠
Blueshift公司通过巧妙地组合材料和层叠技术来定制其热保护系统(TPS)产品,以满足多样化的应用需求。“我们的核心技术被命名为'AeroZero',”Burbey解释道。“我们的产品系列中包括了这项技术的多层叠加版本,例如我们的TripleZero,这是一个三层叠加的产品,总厚度约为20密耳(0.5毫米)。在构建这些层叠结构时,Blueshift采用了我们独有的高温粘合剂。”他还提到,“我们能够根据特定需求定制AeroZero产品,比如在我们的AeroZero-TPS石墨版本中,在顶层添加了石墨层,它作为一种高效的散热器。”石墨层在XY平面上提供卓越的散热性能,而AeroZero层则显著减缓了沿Z轴方向的热量渗透,这种结构设计确保了在极端热环境下的卓越保护效果。
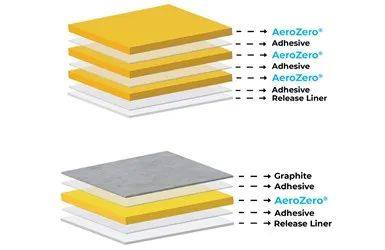
图3 Blueshift 通过将其 AeroZero 材料层(TripleZero,顶部)与其他材料(如石墨、VDA 聚酰亚胺、金属等)堆叠在一起来定制 TPS 产品
“我们拥有多种超级材料的选择,这使我们能够提供所需的热保护,同时满足其他关键性能要求,”他继续说道,“我们的标准商业产品能够提供宽度达到12英寸(305毫米)的卷筒装材料,但我们正计划扩展到更宽的规格。此外,我们还可以根据需要将材料精确切割成4毫米甚至更窄的宽度,以适应各种精细的应用场景。这种灵活性确保我们的产品能够满足客户多样化的需求。”
这又引出了Blueshift材料如何与复合材料部件的集成以及其表面处理的问题。Blueshift的TPS系列产品配备了一种耐高温的压敏胶粘剂,使得应用过程变得简便快捷。“这些材料实际上是即剥即贴型的,”Burbey解释说。
“我们的系统通常在复合材料固化过程之后应用,这种方式非常有利,因为我们无需担心材料在成型过程中的处理方式或其与树脂的相容性。”他进一步指出,Blueshift的TPS几乎可以应用于任何基材,只要这些基材经过适当的预处理,能够提供干净且光滑的表面。而且,胶粘剂的永久粘接强度通常在应用后的24小时以上就能达到,确保了材料的长期稳定性和可靠性。
材料的即剥即贴特性极大地简化并加快了TPS的实际应用流程,同时,材料的柔韧性和纤薄度也为工程师们提供了更大的设计灵活性。“航天工业便是一个鲜明的例子,”Burbey指出,“在追求更可持续的太空探索解决方案的进程中,一些公司已经开始研发可重复使用的火箭,其中保护底层的碳纤维复合材料是至关重要的一环。
与传统用于旧式太空飞行器的软木TPS解决方案相比,基于AeroZero技术的TPS应用过程更为简洁,能够更加轻松地准备发射载具。此外,我们的材料重量仅为传统软木塞材料的一小部分,且能够在火箭上升和重返大气层期间(面对高达2400ºC且持续1-2分钟的极端温度条件)保持性能和耐受力。”这种创新的材料解决方案不仅提升了效率,也对减轻航天器的负载、提高其环境友好性起到了关键作用。
Burbey强调,Blueshift公司生产自己的聚酰亚胺树脂,这一举措是为了满足特定的技术需求。“我们的生产工艺是垂直整合的,从树脂合成、气凝胶制备到粘合剂开发,再到层压和最终的零件切割,整个流程都是我们自己控制的。”他解释道。
对于Blueshift而言,制造零件不仅仅是将TPS切割以适应复杂的结构,尽管材料是以连续的卷对卷方式生产的,但大多数客户选择购买切割好的零件。
“我们能够提供复杂形状和定制设计,”Burbey提到,并以月球着陆器的独特部件为例。“客户通常会提供所需的形状和尺寸,我们使用配备有多种刀片的大型自动切割台来精确切割TPS。此外,我们也有一些项目,我们会直接在客户现场应用我们的TPS,然后将成品运回给他们。”这种服务不仅展示了Blueshift在材料制造上的灵活性,也体现了其在客户服务上的个性化和专业性。
未来应用
Blueshift公司以其轻质结构的热保护系统(TPS)在多个领域取得了显著成就,其应用范围广泛,从电动飞机、太空飞行器和卫星,到高端医疗设备。AeroZero TPS的另一个重要应用是在电池盒领域,它有助于降低电池热失控的风险,这一需求随着对更高功率密度电池需求的增长而日益增加。制造商正在开发更为紧凑的电池组,这些电池组由袋装或圆柱形电池单元组成,它们被组装成小模块,随后堆叠成复杂的电池系统。然而,随着对高功率密度的限制,热失控的风险也随之上升。
为了应对这一挑战,AeroZero TPS的特定变体已经被集成到电池模块和外壳的内外壁中,目的是帮助减缓火灾或爆炸的蔓延,以及控制温度的急剧上升。AeroZero TPS已经证明了其卓越的耐热性能,能够承受高达1000°C的直接火焰长达60分钟而不燃烧。目前,它正在被集成到多种系统中,这些系统旨在提高乘客的安全水平。Blueshift的TPS技术不仅提升了产品的安全性,也推动了在严苛环境下电池技术的发展和应用。
在航空航天领域,Blueshift的TPS技术同样为解决设计师面临的挑战提供了强有力的支持。例如,减重在实现可重复使用的运载火箭方面发挥着至关重要的作用,同时,将重型、高功率密度的电池组集成到电气化飞机中也是当前的重要课题。
为了满足这些需求,必须开发出超越传统、几十年前解决方案的新型材料技术。这不仅要求材料具备优异的热保护性能,还需要在重量、柔韧性和整体性能之间实现精细的平衡。Blueshift的AeroZero TPS正代表了这种平衡的典范,它通过创新的材料解决方案,为航空航天工业带来了前所未有的设计自由度和性能提升。
“我们成立Blueshift的初衷是认识到这项技术在应对行业挑战方面的巨大潜力,并致力于推动正在进行的移动性革命,”Burbey表示。“我们正在助力各公司在一些最具挑战性的应用领域取得突破性的成功。我们将持续扩展我们的能力,并不断追求创新与发展,为未来的复合材料应用提供更加先进的解决方案。”这表明Blueshift公司不仅在现有市场中确立了自己的地位,而且还在积极塑造复合材料技术的未来。
原文链接: https://www.compositesworld.com/articles/structured-air-tps-safeguards-composite-structures
原文始发于微信公众号(艾邦气凝胶论坛):Blueshift 研发出新型空气+聚酰亚胺气凝胶材料,适用于极端温度环境